shed building list
Thursday, November 21, 2024
Free Pallet Shed Plans: Create a Functional Shed for Your Backyard

Free Pallet Shed Plans: Create a Functional Shed for Your Backyard
Tired of clutter piling up in your garage or overflowing from your garden shed? Yearning for a stylish and practical storage solution that won't break the bank? Look no further! This guide provides you with free pallet shed plans, empowering you to build a functional and attractive backyard shed using reclaimed pallets. We'll walk you through the entire process, from sourcing materials to the final touches, transforming those discarded pallets into a valuable asset.
Gathering Your Materials: The Foundation of Your Pallet Shed
Before you even think about hammering a nail, you need to gather your materials. This project thrives on recycling, so the star of the show is, of course, reclaimed wooden pallets. Inspect them carefully; choose sturdy pallets free of rot, significant damage, or embedded nails that could pose safety hazards. You'll need a sufficient number to construct the walls and roof. Beyond the pallets, gather essential supplies like:
- Screws and Nails: Opt for exterior-grade screws and galvanized nails to ensure longevity.
- Wood Primer and Paint/Stain: Protect your pallet shed from the elements and personalize its appearance with a durable coat of paint or stain.
- Plywood or OSB: This is crucial for creating a strong and weather-resistant roof and potentially for sheathing the walls for a more finished look.
- Roofing Material: Consider asphalt shingles, corrugated metal, or even recycled plastic roofing sheets for a durable and watertight roof.
- Tools: You'll need basic carpentry tools including a hammer, screwdriver (or drill), saw, measuring tape, level, and safety glasses.
Construction: Building Your Pallet Shed Step-by-Step
Creating the Foundation
Start by preparing a level base for your shed. This can be a simple concrete slab, a compacted gravel base, or even a level area of packed earth. The stability of your foundation directly impacts the longevity and structural integrity of your shed. Ensure the base is large enough to accommodate the dimensions of your planned shed. A slight overhang will provide protection to the walls from rain splash-back.
Assembling the Walls
Carefully dismantle any unusable parts of the pallets. Clean the remaining wood and assess its structural integrity. Begin constructing your walls by securely fastening pallets together vertically or horizontally, depending on your chosen design. Use screws for a stronger and more durable bond than nails. Remember to check the level and squareness of your walls frequently throughout the construction process to ensure a stable structure.
Constructing the Roof
Once the walls are erected, build the roof frame using additional wooden beams or repurposed pallet sections. You'll need to create a sturdy frame capable of supporting your chosen roofing material. Ensure the roof has a sufficient slope to allow rainwater to run off effectively. Finally, attach the chosen roofing material securely, creating a waterproof and weatherproof seal.
Adding Finishing Touches
Once the main structure is complete, add the finishing touches. This could include adding a simple door, windows for ventilation and natural light (using reclaimed materials where possible), and even shelving inside. A final coat of paint or stain will not only protect the wood but also enhance the aesthetic appeal of your pallet shed, transforming it from a simple storage space into a charming addition to your backyard. Consider adding a weatherproof sealant for ultimate protection.
Safety First: Essential Precautions
Safety should always be your top priority. Wear safety glasses and work gloves throughout the entire construction process. Handle pallets carefully as nails and splinters can cause injuries. If youâre unsure about any aspect of the construction, consult with a qualified professional before proceeding.
Building a pallet shed is a rewarding project that blends sustainability with practicality. By following these free pallet shed plans, you can create a functional and attractive storage solution without emptying your wallet. Enjoy the process and the satisfaction of transforming discarded materials into a valuable asset for your backyard!
How to Build a Rustic 10x12 Pallet Shed with Repurposed Materials
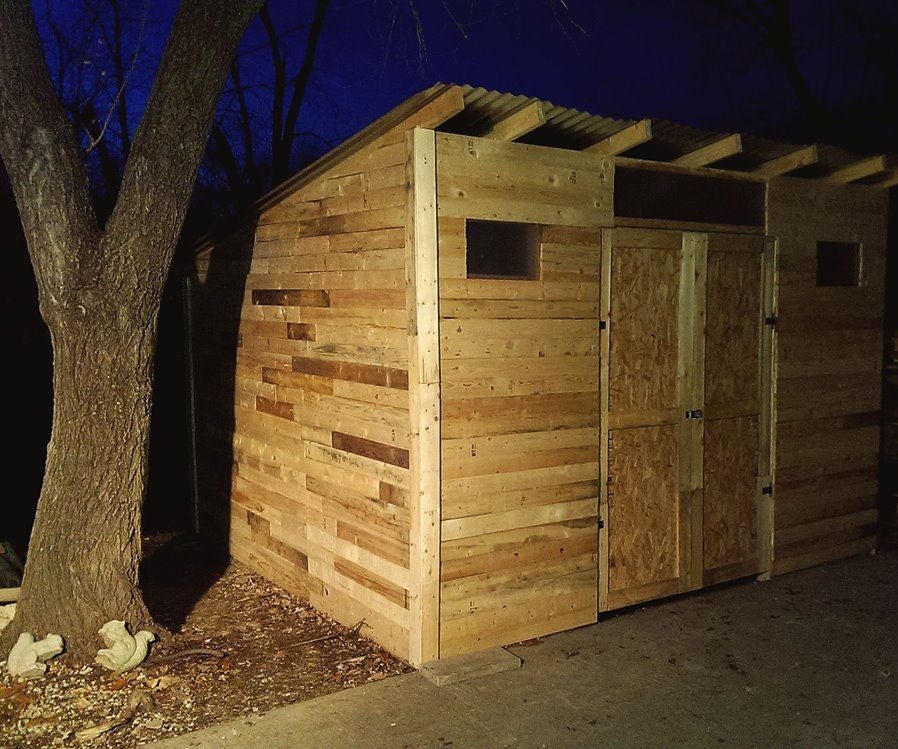
Building Your Dream Rustic 10x12 Pallet Shed: A Repurposed Paradise
Hey there, fellow DIY enthusiasts! So, you're dreaming of a rustic shed, a charming little sanctuary in your backyard, and you want to build it yourself using reclaimed materials? Fantastic! Building a 10x12 pallet shed is a totally doable project, even for someone with moderate DIY skills. It's a great way to save money, be environmentally conscious, and end up with a truly unique structure. Let's dive in and explore how to bring your vision to life!
Planning Your Pallet Paradise: The Foundation
Before you start hammering away, a little planning goes a long way. This isn't rocket science, but some forethought will save you headaches down the line. First, you've got to decide on the location. Consider sunlight, drainage, proximity to your house, and any local building regulations. You'll also want to check with your homeowner's association if applicable.
Choosing Your Palettes
Now for the fun part â" sourcing your palettes! The quality of your pallets is crucial. Look for sturdy pallets made of heat-treated lumber (look for the HT stamp). Avoid pallets that show signs of significant rot, insect damage, or chemical treatments you're not comfortable with. Check with local businesses â" construction sites, grocery stores, and even breweries are often happy to give away their used pallets. Just make sure to get permission first!
Gathering Your Tools and Materials
Beyond the pallets themselves, you'll need a few essential tools and materials. Don't worry, you probably have some of these already! Here's a basic list:
- Measuring tape
- Level
- Hammer
- Saw (circular saw or hand saw)
- Screws (exterior-grade, galvanized are best)
- Drill with drill bits
- Safety glasses
- Work gloves
- Post hole digger (if you're building on posts)
- Concrete mix (if you're using a concrete foundation)
- Optional: Nail gun (speeds things up considerably)
- Optional: Reclaimed wood for trim and accents
Remember, this is a rustic shed. Perfection isn't the goal. Embrace the imperfections of the reclaimed wood â" they add to the charm!
Building the Foundation: Setting the Stage
Your foundation is the backbone of your shed. You have a couple of options:
Option 1: Concrete Slab
This is the most durable option, but it's also the most labor-intensive. You'll need to dig out the area, level the ground, create a formwork, and pour the concrete. Let it cure completely before moving on. This is probably best for heavier items stored in the shed.
Option 2: Pressure-Treated Wood Posts
A more affordable and quicker option. Dig holes for your posts, set them in concrete, and level them carefully. Make sure theyâre deeply enough set into the ground to provide adequate support for the weight of the shed.
Framing Your Pallet Masterpiece
Once your foundation is solid, it's time to start building the frame of your shed. This involves using the pallets to create the walls. This will require some creativity, as pallets aren't standardized and will need adjusting.
Wall Construction
Carefully assess your pallets. Some might be damaged and unusable for load bearing. You'll likely need to disassemble some pallets to get the wood you need and get the framing right. Start by creating a frame for each wall using the sturdiest pallet planks. You can then attach the rest of the pallets to this frame to create the walls. Make sure to reinforce any weak points with additional bracing.
Roof Construction
For the roof, you can get creative. You could use more pallets, but that can add significant weight and might require more structural support. A more straightforward approach might be using plywood or even tarps for the roof structure if you want to keep things simpler and lighter.
Adding the Finishing Touches: Rustic Charm
With the basic structure complete, it's time to add those rustic finishing touches. This is where your creativity really shines! Consider adding reclaimed wood trim around the windows and doors, perhaps even a decorative gable. A coat of weather-resistant sealant will help protect your shed from the elements and enhance its rustic appeal. Don't forget a sturdy door â" you could even repurpose an old door from a salvage yard!
Personalizing Your Shed
This is your chance to make this shed uniquely yours. Add some shelves inside, perhaps create a small workbench, or even paint it a fun color that complements your yard. You can add some vintage signs or other rustic décor to personalize the space.
Commonly Asked Questions
Q: How long will this project take?
A: This really depends on your experience and how much time you can dedicate to it. Expect to spend several weekends, maybe even a couple of weeks, if you're doing it yourself.
Q: How much will this cost?
A: The beauty of this project is that it can be very affordable. The biggest expense will likely be the screws, sealant, and any additional materials you need beyond the pallets themselves. Your costs will vary greatly depending on your location and materials used.
Q: Do I need any special permits?
A: Check with your local authorities. Depending on your location and the size of your shed, you may need a permit. Itâs better to be safe than sorry and check beforehand!
Q: What if I'm not very handy?
A: Don't worry! This project is designed to be approachable for DIYers of all skill levels. There are tons of online resources and videos to guide you through each step. Don't be afraid to ask for help from friends or family if you get stuck!
There you have it! Building a rustic pallet shed is a rewarding project that combines creativity, resourcefulness, and a whole lot of fun. Get started on your dream shed today!
Wednesday, November 20, 2024
Transform an Empty Corner Into a Lean-To Shed with These Simple Plans

Transform an Empty Corner Into a Lean-To Shed with These Simple Plans
Tired of clutter piling up? Wish you had a little extra storage space, but lack the budget or expertise for a full-blown shed construction? Then consider transforming that neglected corner of your yard into a practical and attractive lean-to shed! This project, achievable even for novice DIYers, offers a surprisingly spacious storage solution with minimal materials and effort. Follow these simple plans and watch your empty corner blossom into a functional addition to your property.
Planning Your Lean-To Shed
Before you grab your tools, careful planning ensures a successful project. First, choose your location wisely. Consider proximity to your house for easy access, existing structures that can serve as support, and adequate sunlight for drying materials if necessary. Next, determine the dimensions. A lean-to's size depends on your storage needs and available space. Sketch a simple plan, noting the desired length and width, along with the height at the peak of the roof. Finally, acquire necessary permits. Local building codes vary; check with your municipality to confirm if permits are required for your lean-to shed project and acquire them before commencing construction.
Gathering Your Materials
This project emphasizes simplicity and affordability. Your material list will include pressure-treated lumber for durability, roofing materials (consider asphalt shingles for ease of installation), screws or nails, concrete blocks (or alternative anchoring system) for the base, and a level to ensure a stable structure. Don't forget essential safety gear like safety glasses and work gloves! A detailed list, based on your shed's dimensions, should be compiled before heading to your local hardware store. Remember to consider the weight your lean-to will bear â" selecting robust materials is crucial for longevity.
Detailed Materials List (Example for a 6ft x 4ft Shed):
- Four 6ft pressure-treated 4x4 posts for the base.
- Six 6ft pressure-treated 2x4s for the frame.
- Several 6ft pressure-treated 2x4s for roofing support rafters.
- Plywood or OSB sheeting for walls (optional).
- Asphalt shingles or other roofing material.
- Concrete blocks or other anchoring system.
- Screws or nails, appropriate for the wood type.
- Level, measuring tape, saw.
Step-by-Step Construction
Begin by preparing the base. Level the ground where your shed will be placed and set your concrete blocks or other anchoring system for the base. These will firmly anchor your 4x4 posts, which will form the foundation of your lean-to. Next, construct the frame. Attach the 2x4s to the posts, ensuring squareness and stability. This creates the skeleton of your lean-to. Now, add the roofing supports â" these rafters should be properly spaced and securely attached to the frame to support the weight of the roofing material. Finally, install the roofing, carefully overlapping the shingles to ensure a weathertight seal. You can add optional walls using plywood or OSB for extra privacy and storage.
Finishing Touches and Considerations
Once the construction is complete, consider adding a simple door for easy access. This can be as simple as a framed opening covered with plywood and hinges. Think about adding weather stripping around the door and along the base to prevent drafts and moisture. Painting the shed adds both aesthetic appeal and protection from the elements. A coat of exterior-grade paint or stain will significantly extend the life of your lean-to. Remember to regularly inspect your shed for any signs of wear and tear and address them promptly to maintain its structural integrity. With a little care and maintenance, your DIY lean-to shed will provide years of reliable storage.
Saturday, November 16, 2024
Designing a Lofted Shed with 12x20 Plans for Storage and Function

Building Your Dream 12x20 Lofted Shed: Storage, Space, and So Much More!
So, you're thinking about building a shed? Fantastic! But not just *any* shed â" you want a 12x20 lofted shed, maximizing space and functionality. Thatâs awesome! This is a project that can really transform your property, adding valuable storage and maybe even a fun little workshop space. Let's dive into the exciting world of lofted shed design and construction.
Planning Your 12x20 Lofted Shed Masterpiece
Before you even think about grabbing a hammer, careful planning is key. This isn't about slapping together some boards; we're talking about building something sturdy and useful that will last for years. Think of it as a mini-construction project!
Choosing the Right Location
Where will your magnificent shed reside? Consider these factors:
- Accessibility: Will you need a vehicle to access it? Make sure there's enough space for maneuvering.
- Sunlight: Do you need natural light for a workshop? Consider sun exposure when choosing your spot.
- Drainage: Avoid low-lying areas prone to flooding. Youâll want a dry foundation.
- Utilities: If you're planning on electricity or running water, consider proximity to existing lines. This might affect your final location choice.
- Local Regulations: Check with your local council or homeowner's association about building permits, setbacks, and any restrictions on shed size or design.
Designing for Function
Think about how you plan to use your shed. This will drastically influence the design. Will it be primarily for storage, or will you have a workshop area? Maybe even a small potting shed? Knowing this will help you decide on things like:
- Loft Access: Will you need a fixed staircase, a pull-down ladder, or something else entirely?
- Window placement: More windows mean more light, but also less wall space for shelving.
- Door placement and size: Consider the size of items you'll be storing or moving in and out of the shed.
- Workbenches and shelving: Plan the layout carefully, thinking about workflow and accessibility.
Materials: Building the Foundation
Choosing the right materials is crucial for longevity and durability. Let's talk about the main players:
- Foundation: A concrete slab provides a solid, level base. Gravel foundations are also a viable, albeit less expensive option. But remember that a poor foundation can lead to issues down the line.
- Framing: Pressure-treated lumber is your friend. It's resistant to rot and insects, essential for a long-lasting shed.
- Siding: Vinyl, metal, or wood â" the choice is yours. Each material has its pros and cons regarding cost, maintenance, and aesthetics. Metal is highly durable and low maintenance, while wood offers a more rustic look.
- Roofing: Asphalt shingles are a popular and relatively inexpensive choice. Metal roofing is another durable option, offering superior protection from the elements.
Construction: Building Your 12x20 Shed
This part's exciting, but remember safety first! If you're not confident in your DIY skills, consider hiring a professional. Otherwise, let's get building!
Step-by-Step Guide (Simplified!):
This is a high-level overview â" each step involves numerous sub-steps. Always refer to detailed plans and tutorials.
- Foundation: Prepare your chosen foundation, ensuring it's level and solid.
- Framing: Construct the walls and roof frame, ensuring squareness and proper bracing.
- Sheathing: Install sheathing (plywood or OSB) over the framing for added strength and a surface to attach siding to.
- Siding and Roofing: Install your chosen siding and roofing materials, following manufacturer instructions carefully.
- Loft Construction: Build the loft floor joists and decking, ensuring proper support and access.
- Finishing Touches: Install doors, windows, trim, and any interior features.
Important Considerations During Construction:
- Building Codes: Adhere to all local building codes and regulations.
- Safety First: Wear appropriate safety gear, including safety glasses, gloves, and hearing protection.
- Weather Conditions: Work on dry days when possible. Rain can significantly delay the project and damage materials.
- Take Breaks!: Building a shed is hard work. Take regular breaks to avoid fatigue and injury.
Adding the Finishing Touches to Your Shed
Once the structure is up, the fun part begins! Personalizing your shed makes it truly yours.
Interior Design and Organization
Think about your storage needs and how to maximize the space. Shelving, pegboards, and cabinets can help keep things organized and easily accessible. If you're using the space as a workshop, consider dedicated areas for tools and projects. Proper lighting is also essential, no matter the use.
Exterior Aesthetics
Consider adding some landscaping around your shed to make it blend seamlessly with your property. A simple paint job can transform the look and feel, and adding decorative elements such as shutters or a weather vane can add personality.
Commonly Asked Questions
Let's tackle some frequently asked questions about 12x20 lofted sheds.
Q: How much does it cost to build a 12x20 lofted shed?
A: Costs vary widely depending on materials, location, and labor. Expect to spend anywhere from $3,000 to $10,000 or more. Using more affordable materials and doing the work yourself will significantly lower costs.
Q: Do I need a building permit?
A: This depends entirely on your local regulations. Check with your local council or homeowner's association before you start building.
Q: How long does it take to build a 12x20 lofted shed?
A: This varies greatly depending on experience, the complexity of the design, and weather conditions. Expect it to take anywhere from a few weekends to several weeks, even months for those new to construction.
Q: What are the best materials for a lofted shed?
A: Pressure-treated lumber for framing, metal or vinyl siding for durability, and asphalt or metal roofing are all popular choices. The best choice depends on your budget, aesthetic preferences, and climate.
Q: Can I add electricity to my shed?
A: Yes, but this requires an electrician to ensure it's done safely and to code. You'll likely need to obtain additional permits.
Building a 12x20 lofted shed is a rewarding project. With careful planning, attention to detail, and a bit of elbow grease, you'll create a valuable addition to your property that youâll enjoy for years to come!
Monday, November 11, 2024
How to Build a Pole Barn with a Pre-Cut Kit for Quick Assembly
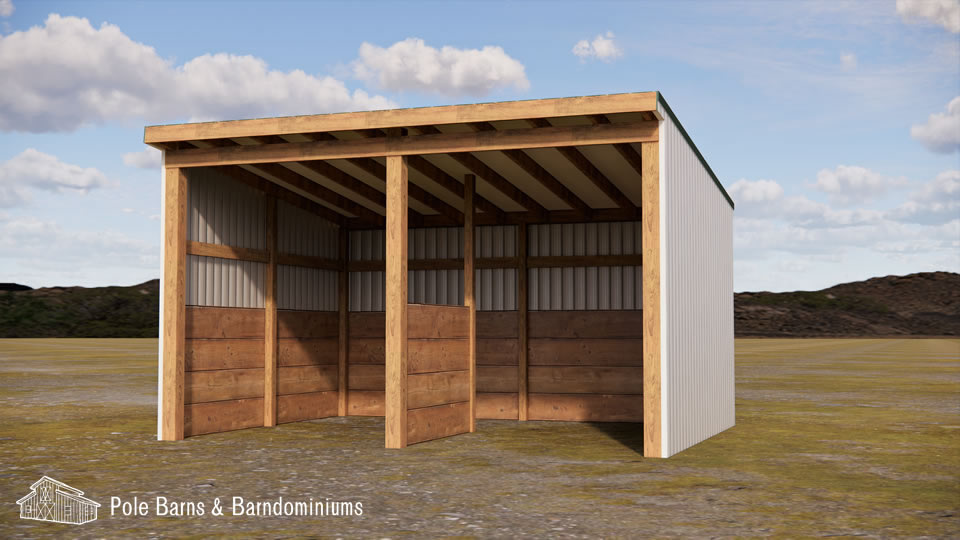
Alright, so you've decided to go for it - you're building a pole barn! That's awesome. You're joining the ranks of DIYers who love the freedom and satisfaction that comes with building something yourself.
And you've chosen a pre-cut kit? Smart move! It takes a lot of the guesswork out of the project and speeds things up. But let's be real, "quick" and "weekend" are relative terms when it comes to building. But hey, with a little planning and a good crew (or a really dedicated friend), you can get a roof over your head (or your equipment) in a reasonable amount of time.
Here's a breakdown of what you need to know to build your pole barn:
1. The Basics - Planning and Preparation
First things first, you need to do your homework. This is where you lay out the foundation for your project, literally and figuratively.
Get the Right Permits: Before you even think about digging a hole, check with your local building department. They'll tell you what permits you need, any specific building codes you have to follow, and maybe even offer some helpful tips. It's better to be safe than sorry, right?
Choose Your Kit: There are tons of options when it comes to pre-cut pole barn kits. You can get kits for simple structures to kits that include everything you need for a full-fledged workshop or garage. Decide what size, features, and materials you need. This will help you narrow down your choices and find the right kit for your needs.
Site Prep: This is where the fun begins! You need to clear the area where your barn will be built. Remove trees, rocks, and anything else that might get in your way. You'll also need to level the ground and compact it for a solid foundation. If you're in a hilly area, you might need to do some grading.
Setting the Foundation: This is where you'll dig those holes! You'll need to create sturdy footings for your pole barn. The depth and size of the footings will depend on the size of the barn and local soil conditions. Concrete footings are the most common and durable option.
2. Assembling the Frame: The Skeleton of Your Barn
Now it's time to get those poles up!
Erect the Posts: This is where having a good crew comes in handy. You'll need to lift the pre-cut posts into the concrete footings and plumb them carefully. Make sure they're all level and straight! A good level is your best friend here.
Attaching the Beams: Once the posts are secure, you can start attaching the roof beams. This involves lifting the beams and securing them to the tops of the posts. You'll need to make sure the beams are level and properly aligned.
Adding the Braces: Braces provide stability and support to your barn's structure. You'll typically find a variety of bracing elements in your kit. Install them according to the manufacturer's instructions.
Installing the Wall Panels: Depending on the kit, you might have pre-made wall panels or individual pieces of wall siding. These will be attached to the posts, and often secured with a variety of fasteners.
3. Roofing and Finishing Touches:
Roofing: Once the frame is complete, it's time for the roof. Most kits come with pre-cut roof trusses and plywood sheathing. Install the trusses and sheathing, then you can move on to the roofing material. The type of roofing you choose will depend on your budget and the climate where you live.
Doors and Windows: Now you'll install doors and windows. This is a good time to check and double check that your openings are the correct size and that you have everything you need to get them installed.
Siding and Trim: The final step is adding the siding and trim. This is where you can personalize your pole barn and give it that final touch. Again, the kit you choose will often determine the types of siding and trim that are included.
4. Safety First and Always
Let's be real - working with wood, power tools, and a whole lot of weight can be dangerous if you're not careful.
Wear Proper Safety Gear: This includes safety glasses, hearing protection, work gloves, and steel-toe boots.
Use Tools Safely: Make sure you know how to use all of the tools you're working with, and follow the manufacturer's instructions.
Don't Take Shortcuts: This is not the time to be impatient. Take your time and do everything carefully. A little extra time spent getting things right can save you a lot of hassle in the long run.
5. Tips for Success
Read the Instructions: This might sound obvious, but it's important to carefully read the instructions that come with your kit. They'll provide step-by-step guidance and helpful tips.
Have the Right Tools: Make sure you have all the necessary tools before you start building. This might include a level, hammer, saw, drill, tape measure, and safety gear.
Plan Your Work: Before you start building, it's a good idea to sketch out a rough plan of how you'll assemble the barn. This will help you visualize the process and make sure you have everything you need.
Ask for Help: Don't be afraid to ask for help if you need it. There are plenty of resources available online and in your community.
Building a pole barn from a pre-cut kit is a great way to save time and money. It's also a fun and rewarding project that can help you improve your DIY skills.
So, go get that kit, gather your friends, and start building! Just remember to be safe, take your time, and enjoy the process.
How to Build a Pole Barn with a Large Overhang for Extra Protection
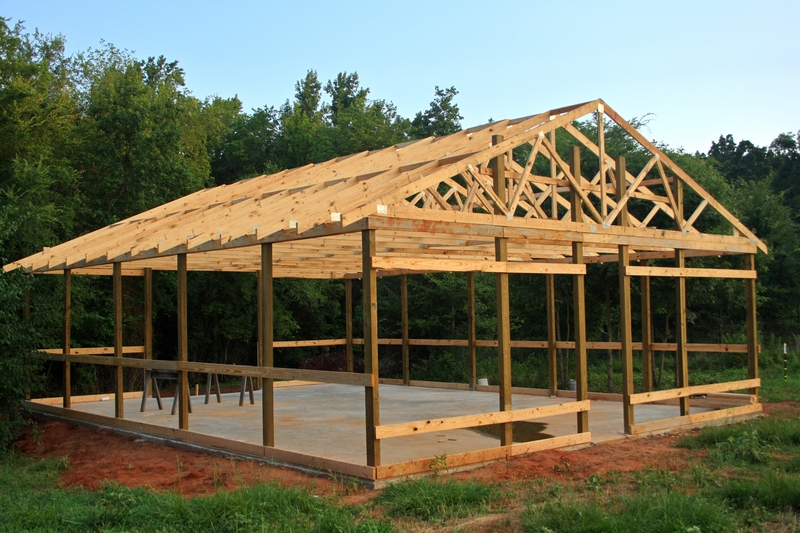
Pole barns, with their straightforward construction and adaptable design, are popular structures for a multitude of purposes, from workshops and garages to livestock shelters and storage facilities. A key element often overlooked in their design, however, is the potential for extended overhangs. A large overhang not only adds aesthetic appeal but also serves as a significant protective element for the structure and its contents. This article will delve into the intricacies of building a pole barn with an expansive overhang, offering comprehensive guidance on design, materials, and construction techniques.
Design Considerations:
1. Purpose and Usage: Before embarking on the project, it is crucial to define the intended use of the pole barn. This will inform critical aspects of the design, including the size, height, and overall configuration of the overhang. A workshop may require a larger overhang than a simple storage shed, and a livestock shelter may necessitate a more robust design.
2. Local Regulations and Building Codes: Each municipality has specific codes and regulations governing building structures. Research local building codes prior to design and construction to ensure compliance and avoid costly setbacks. This includes factors such as minimum distance from property lines, required foundation types, and permitted roofing materials.
3. Site Conditions: The site where the pole barn will be erected plays a critical role in the design. Factors such as soil type, terrain, and existing utilities must be considered. Additionally, the presence of trees, power lines, or other obstacles should be factored in to prevent interference with the structure.
4. Overhang Size and Shape: The size and shape of the overhang are crucial for its effectiveness. A wider overhang offers greater protection from rain, snow, and sun, while a deeper overhang provides more shelter for vehicles or equipment. Consider the intended use and the prevailing weather conditions when determining the desired size and shape. A common approach is to extend the roofline beyond the wall by 2-3 feet for basic protection, while larger overhangs may extend up to 5-6 feet.
5. Roofing Materials and Pitch: The roofing material selected for the overhang will greatly influence its durability, aesthetics, and cost. Consider factors such as weight, weather resistance, and maintenance requirements. The roof pitch also plays a crucial role in snow and rainwater drainage. A steeper pitch, typically 6:12 or greater, promotes efficient water runoff and prevents snow accumulation.
6. Foundation and Support Structure: The foundation must be designed to accommodate the added weight and load of the overhang. Concrete piers or footings are common foundation choices for pole barns. The support structure, typically consisting of beams and posts, must be robust enough to support the overhang's weight and withstand environmental forces. Additional support posts or beams may be required for larger overhangs.
Materials and Construction:
1. Posts: Pressure-treated lumber is the ideal material for the posts, as it resists rot and decay. The size and spacing of the posts will depend on the overall dimensions of the pole barn and the weight of the overhang. Consider using 6x6 or 8x8 posts for larger overhangs.
2. Beams and Trusses: Strong and durable beams are crucial for supporting the roof and overhang. Glulam beams, engineered lumber, or heavy-duty dimensional lumber can be used, depending on the size and load requirements. Consider using trusses instead of beams, particularly for wide overhangs, as they offer superior strength and stability.
3. Roofing System: The roofing system comprises the sheathing, underlayment, and roofing material. For a strong and durable roof, plywood or OSB sheathing is recommended. An underlayment, such as felt or synthetic felt, acts as a barrier against moisture penetration. The chosen roofing material, whether asphalt shingles, metal roofing, or another option, should be compatible with the local climate and building codes.
4. Framing and Siding: The framing for the overhang is typically constructed using dimensional lumber, creating a frame that supports the roof and siding. The siding can be a variety of materials, including wood, metal, or composite, depending on the desired aesthetic and budget.
5. Drainage and Gutters: Proper drainage is essential to prevent water buildup and potential damage to the structure. Install gutters along the edges of the overhang to collect and direct rainwater away from the building. Downspouts should be connected to gutters and extend to the ground to prevent water from pooling around the foundation.
Construction Steps:
1. Site Preparation: Clear the site of vegetation and debris, and level the ground for the foundation. Ensure proper drainage to prevent water from pooling near the structure.
2. Foundation Installation: Install the foundation according to the design specifications and local building codes. Concrete piers or footings are commonly used for pole barn foundations.
3. Post Erection: Install the posts at the designated locations, ensuring they are plumb and level. Secure the posts to the foundation using concrete or metal brackets.
4. Beam Installation: Place the beams on top of the posts and securely attach them using brackets or other appropriate methods. Ensure the beams are level and aligned.
5. Roof Construction: Construct the roof system, including sheathing, underlayment, and roofing material. For large overhangs, consider using trusses instead of beams for optimal support.
6. Framing and Siding: Frame the overhang using dimensional lumber, and attach the siding to the frame. Ensure proper ventilation is provided to prevent moisture buildup.
7. Drainage and Gutters: Install gutters and downspouts along the edges of the overhang to direct rainwater away from the building.
8. Finishing Touches: Add finishing touches, such as trim, soffits, and fascia, to enhance the appearance of the overhang.
Benefits of a Large Overhang:
1. Protection from the Elements: A generous overhang provides significant protection from rain, snow, and sun, keeping the structure and its contents dry and cool.
2. Extended Storage Space: The overhang creates additional covered space that can be used for storage, work areas, or recreational activities.
3. Enhanced Aesthetics: A well-designed overhang adds aesthetic appeal to the pole barn, enhancing its overall appearance.
4. Increased Durability: The overhang shields the walls and roof from direct exposure to the elements, extending their lifespan and reducing maintenance requirements.
5. Increased Energy Efficiency: The overhang can provide shade during the summer months, reducing heat gain and lowering cooling costs.
Conclusion:
Constructing a pole barn with a generous overhang requires careful planning, proper materials selection, and skilled craftsmanship. By following the guidelines outlined in this article, homeowners and builders can create a durable and attractive structure that provides enhanced protection and functionality. The benefits of a well-designed overhang extend beyond mere aesthetics, offering practical advantages for a multitude of applications. Investing in a large overhang is a wise decision for those seeking a sturdy, adaptable, and visually appealing pole barn structure.
How to Build a Pole Barn with Custom Wall Features

The classic pole barn design, with its simple construction and versatile application, remains a popular choice for a variety of purposes. However, many seek to elevate this traditional design by incorporating custom wall features, adding both aesthetic appeal and functional enhancements. This article provides a detailed guide to building a pole barn with personalized touches, covering essential steps from planning to execution.
1. Planning and Design:
A. Define the Purpose and Scope:
Functionality: Determine the primary use of the pole barn. Will it be a workshop, a garage, a storage facility, a barn for livestock, or a combination thereof?
Size and Layout: Carefully consider the required square footage and optimize the layout for efficient use of space.
Budget: Set a realistic budget and prioritize features that align with your needs and financial constraints.
B. Explore Custom Wall Features:
Windows and Doors: Consider the size, shape, and placement of windows and doors to maximize natural light, ventilation, and accessibility.
Walls: Explore different wall finishes such as siding, stone, or brick for aesthetic appeal and durability.
Interior Finishes: Plan for interior walls, ceilings, and flooring options that suit your desired ambiance and functionality.
Insulation and Climate Control: Evaluate your climate and consider the level of insulation required for comfort and energy efficiency.
C. Secure Necessary Permits:
Contact your local building department to obtain all required permits and ensure compliance with local codes.
Be prepared to provide detailed plans, specifications, and engineering calculations for review.
2. Site Preparation and Foundation:
A. Site Selection:
Choose a level site with adequate drainage to prevent water accumulation around the building.
Ensure access for construction vehicles and the delivery of materials.
B. Foundation Construction:
Concrete Piers: Concrete piers are the most common foundation type for pole barns. They are durable, economical, and require less excavation.
Precast Concrete Columns: Precast concrete columns offer a quicker construction process and can be tailored to specific design requirements.
Steel Posts: Steel posts provide strength and durability but require proper treatment for corrosion resistance.
3. Framing and Roof Construction:
A. Framing:
Posts: Use pressure-treated lumber or steel posts for the structural framework.
Beams: Securely attach beams to the posts to support the roof and walls.
Rafters: Construct the roof framing with rafters that span the beams and provide support for the roof sheathing.
B. Roof Construction:
Sheathing: Install roof sheathing over the rafters to provide a solid base for roofing materials.
Roofing: Choose a roofing material that suits your budget, aesthetic preference, and climate.
Ventilation: Ensure proper ventilation to prevent moisture buildup and maintain a comfortable interior temperature.
4. Custom Wall Construction:
A. Exterior Walls:
Framing: Build the wall framing using studs and bracing.
Insulation: Install insulation within the wall cavities to enhance energy efficiency and reduce noise.
Sheathing: Cover the framing with sheathing to provide a smooth surface for the exterior finish.
Exterior Finish: Choose a siding material that complements your design and offers desired durability.
B. Interior Walls:
Framing: Construct interior wall framing using studs and bracing.
Insulation: Install insulation within the wall cavities for thermal comfort and noise reduction.
Interior Finish: Apply desired interior finishes such as drywall, paneling, or other options that meet your design and functional needs.
5. Windows and Doors:
A. Window Installation:
Carefully measure and cut openings in the walls for windows.
Install windows using flashing and sealant to ensure proper water resistance.
Consider the type and size of windows based on desired light and ventilation.
B. Door Installation:
Prepare the door openings in the walls.
Install doors using hinges, latches, and weatherstripping for smooth operation and weatherproofing.
6. Finishing Touches:
A. Electrical and Plumbing:
Plan and install electrical wiring, plumbing, and other utilities according to local codes and safety regulations.
Consider the placement of electrical outlets, lighting fixtures, and other necessary features.
B. Flooring:
Install flooring that suits your desired aesthetic and functionality.
Options include concrete, wood, tile, epoxy coatings, and more.
C. Painting and Decorating:
Paint the interior and exterior walls to enhance the aesthetic appeal and provide a protective layer.
Consider adding decorative elements such as trim, moldings, and custom finishes.
7. Final Inspections and Completion:
Conduct thorough inspections of all construction elements to ensure compliance with codes and specifications.
Obtain necessary permits and approvals for occupancy.
Complete all landscaping, site cleanup, and final touches to create a finished and functional pole barn.
Customizing Your Pole Barn:
By incorporating custom wall features, you can create a pole barn that surpasses traditional designs. Here are some ideas:
Custom-designed Windows: Explore unique shapes, sizes, and placements to create a distinctive aesthetic and optimize natural light.
Stone or Brick Accents: Add a touch of elegance and durability with stone or brick veneers for select walls.
Custom-built Doors: Choose unique door styles and materials to create an impressive entrance.
Built-in Storage Solutions: Design custom cabinets, shelves, and storage systems to maximize space efficiency.
Interior Design Features: Incorporate wood paneling, vaulted ceilings, or other unique features to create a personalized ambiance.
Conclusion:
Building a pole barn with custom wall features requires careful planning, attention to detail, and skilled craftsmanship. By following the steps outlined above, you can create a versatile and personalized structure that meets your specific needs and aesthetic preferences. Remember to consult with professionals for design guidance, construction expertise, and code compliance. With careful planning and execution, you can build a pole barn that serves its purpose while standing as a testament to your individual style and vision.